Redesigning a Garden Product to Decrease
Shipping Costs
One of Consolidated Foam’s central products is their Gardien brand Rose Cone—molded polystyrene shells that insulate plants from temperature shifts during the winter. However this design makes them very lightweight and very bulky, resulting in high shipping costs and effectively limiting their distribution to the Midwest.
To resolve this, my Senior Capstone team redesigned the Rose Cone to improve shipping efficiency without compromising the insulation properties.

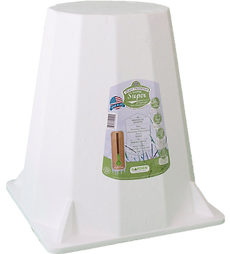
Research:
Evaluating Current Products
Given the importance of thermal regulation, our first focus was on competitive benchmarking evaluating the Gardien cones and comparing their performance to the competition. Our results showed that the Gardien cones were the only product that provided any noticeable reduction in temperature variations.
​
In doing this, we developed a standardized procedure for evaluating thermal performance in comparison to the Gardien cones. We’d test a new design or product alongside existing Gardien cones to produce data that provided a direct comparison of their performance under the same conditions.
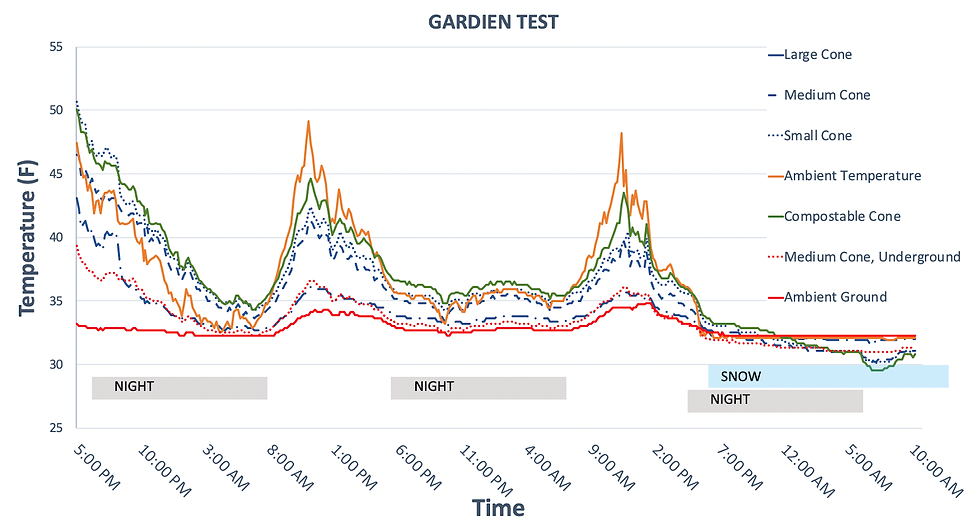


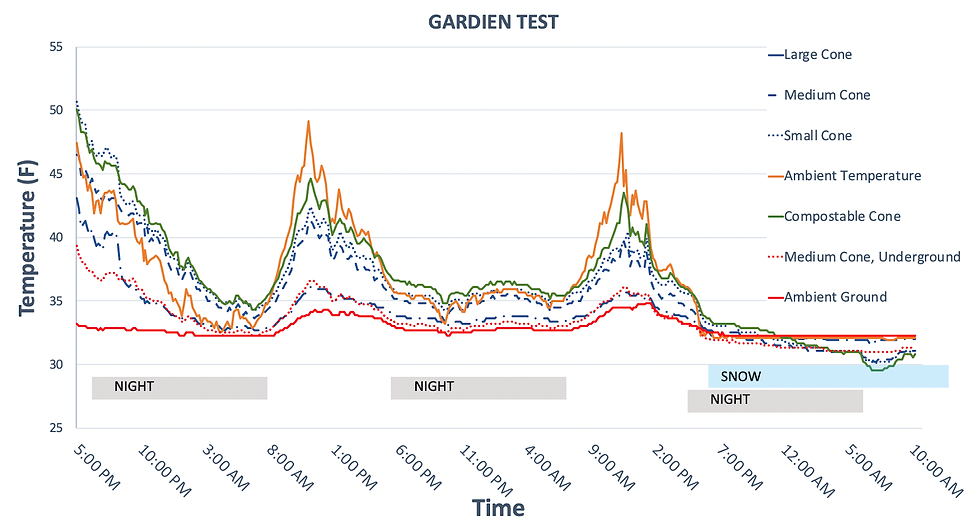
Testing:
Thermal Impact of Design Features
​
Our next step was to research the thermal impact of different design variable and features. In particular, we tested the thermal efficiency of different design profiles and their different surface area to volume ratios. To test this variable, I built three prototypes: a cylinder, a frustum,* and a hemisphere. To ensure comparability of the test results, I designed each prototype with the same internal volume and base area.**
​
*A flat topped cone or pyramid; a cone in this case.
**This ensured each design would start with equal masses of internal air and would have equal air exchange at the base.

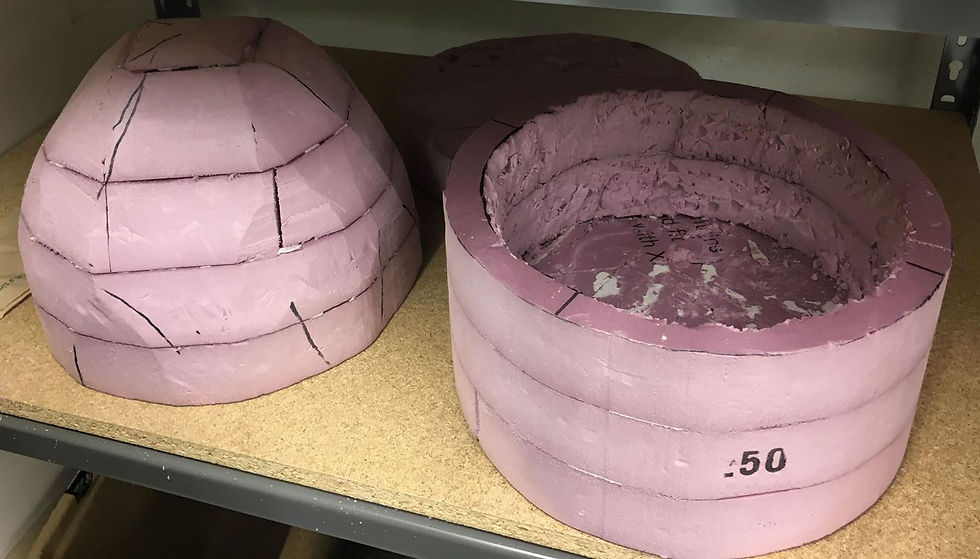
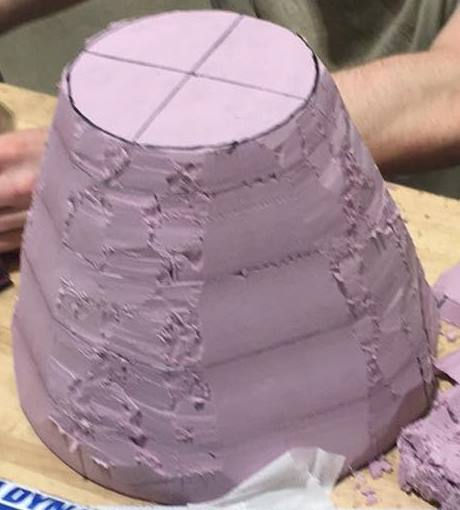

Prototyping:
Concept Generation and Evaluation
Out of an initial 40 brainstormed design ideas, we narrowed down to 5 to explore further. These broadly fell into two categories: either a frame covered with an insulating composite cloth (like what’s used in pizza delivery bags), or stiff foam panels can be assembled into a cone shape.
We tested the thermal performance of several insulating fabrics, finding them to be significantly inferior to the Gardien cones. Based on these results and a weighted evaluation of the other design requirements, we selected a final design.
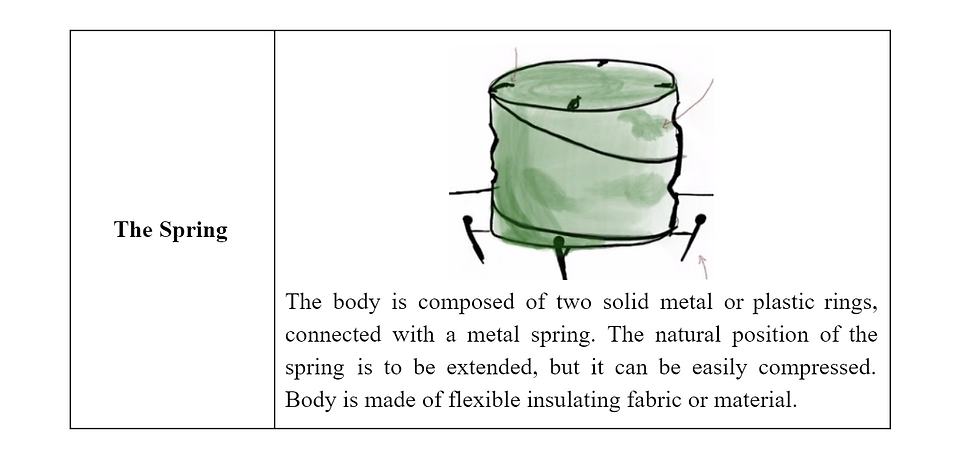

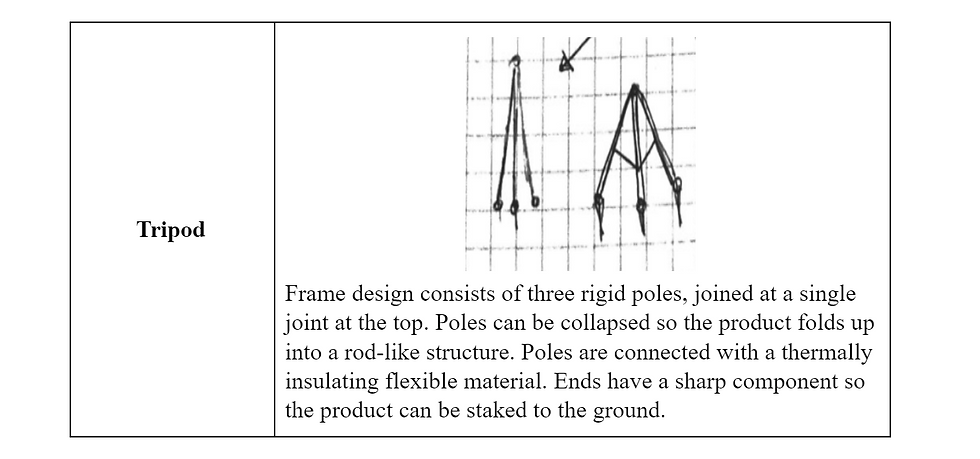
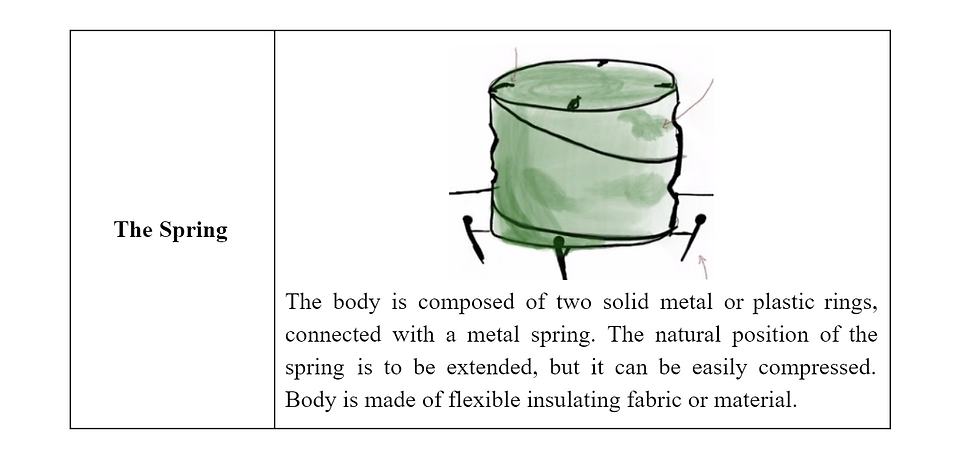
Outcome:
Hook and Loop Folding
Like the original Gardien cone, the final design (and I think it’s worth noting that it was one of my designs) uses polystyrene material, but encases foam panels in a layer of fabric, allowing them to be folded flat for shipping. The panels assemble into a six-sided frustum, which uses hook and loop fasteners to hold its shape.




Outcome:
Final Design Evaluation
The original Gardien cone is a single injection molded piece of foam, which makes it incredibly cheap to manufacture, and allowing it to be sold at a fraction of the price of the competition. Producing a design with a similarly high perfromace to cost ratio was a constant—albeit secondary—concern throughout the project. However, the final design does match up to this standard. A preliminary BOM gave the unit manufacturing cost of $4.86, and thermal testing showed it to be on par with the Gardien products!

This project was challenging, because it required a different way of thinking compared to my previous projects. In most cases, you can deal with each design requirement independently, but in this case, everything was bound up into a single system. Every design choice (material, shape, structure, etc.) influenced both thermal performance and shipping cost. This had a big impact on our process, most notably the extensive thermal testing we did at each step. However, despite this (not to mention the challenges of completing this project in the midst of a global pandemic), I’m quite pleased with how it turned out!