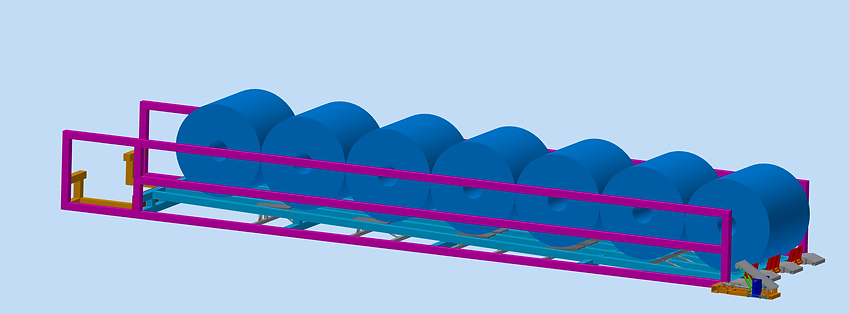
Staging Packaging Rolls on the Factory Floor
To eliminate idle time, Belmark, a packaging company, stages batches of rolls at their machines. But saving time here creates lag as machine operators advance the rows of rolls by hand.
Belmark outsources their engineering design needs, so I was brought on to resolve their material handling problem. I completed the project by developing an efficient design solution.
Immersion:
On the Factory Floor
​
I began my evaluation by spending two weeks working with the machine operators on the factory floor. I learned the process first hand and talked to the operators about the current state of manufacturing.
In addition to the feedback I received, I observed that the material expediters delivering the rolls had to dismount their forklifts to move the rolls into position by hand, adding another source of delay to the process.

Concept:
A Roll Staging Ramp
​
The best solution to the problem was a ramp that could hold a batch of rolls. The high end would have a "dumper" to tip rolls off of their storage pallets, and gravity would automatically advance the line of rolls without the machine operator's help.
-
The ramp needed to be 20 feet long to hold enough rolls but not extend into the aisle between machines
-
It needed to hold the weight of the rolls, and be wide enough to fit the biggest ones they make

Function:
Slowing the Rolls
The rolls are big—up to 1400 lbs and 42” wide, so I needed to stop them from building momentum down the 20-foot ramp.
I designed a series of 5 brakes backed by shock absorbers. A roll would only roll 4 feet before being slowed down again.
​
-
Shock absorbers allow the brakes to handle a range of loads, letting slower and smaller rolls past while still slowing the larger and faster ones
-
I optimized the brake design with regard to the stroke length, damping coefficient, and brake angle
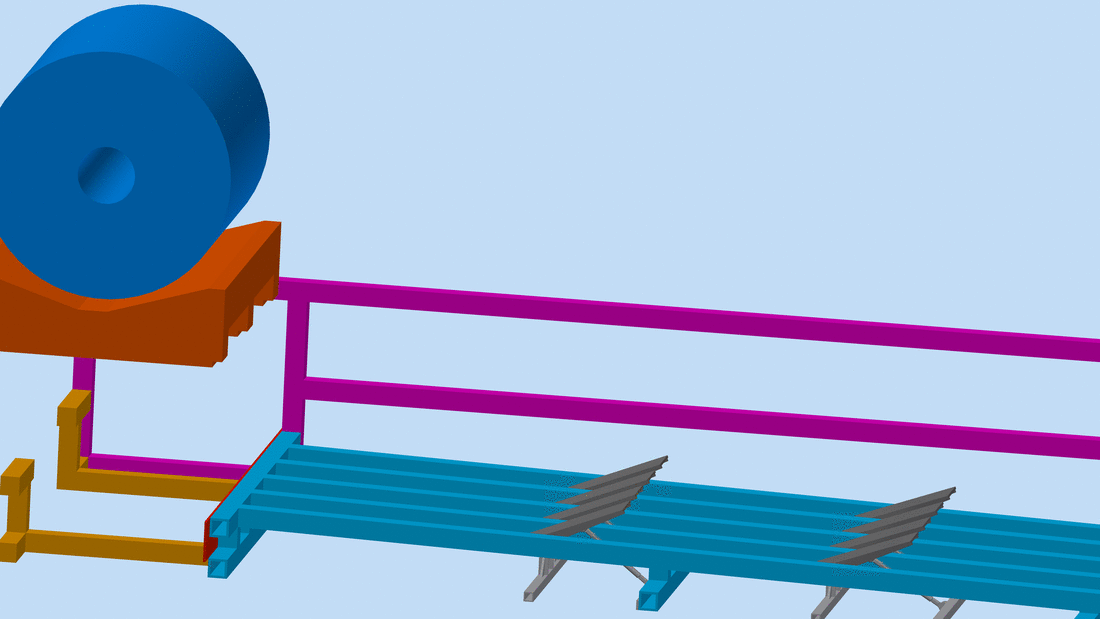
Function:
One Roll at a Time
The ramp had to let one roll off at a time without the ones behind it coming off too. I workshopped several ideas for this function and settled on a pedal-operated barrier.
Disengaging the locking mechanism (dark blue) allows the pedal (grey) to lower the release flaps (red), letting the roll off. Then springs (green) return the system to the locked position before the next roll arrives.
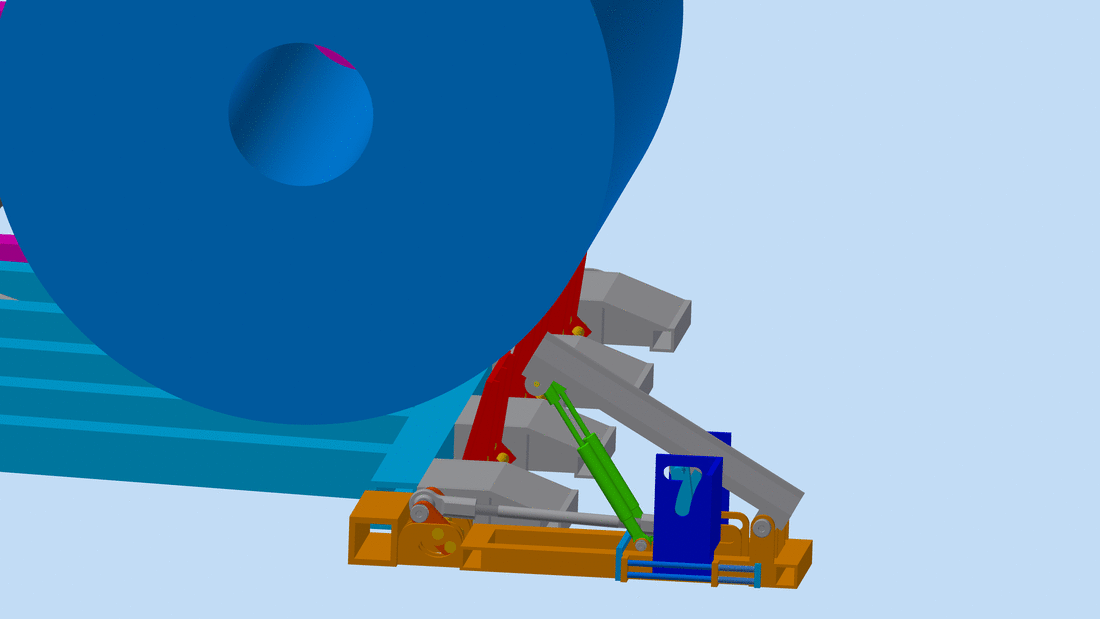
This project was an invaluable experience for me as a young engineer. Working through the summer of 2018, I applied the knowledge I’d learned at Northwestern and gained new professional skills—based on a time and motion study I preformed, my design saves up to 633 man hours of employee labor per year. By the end of the summer, I was able to leave my supervisor with a finalized design, complete with production drawings and detailed notes on my calculations and design process.